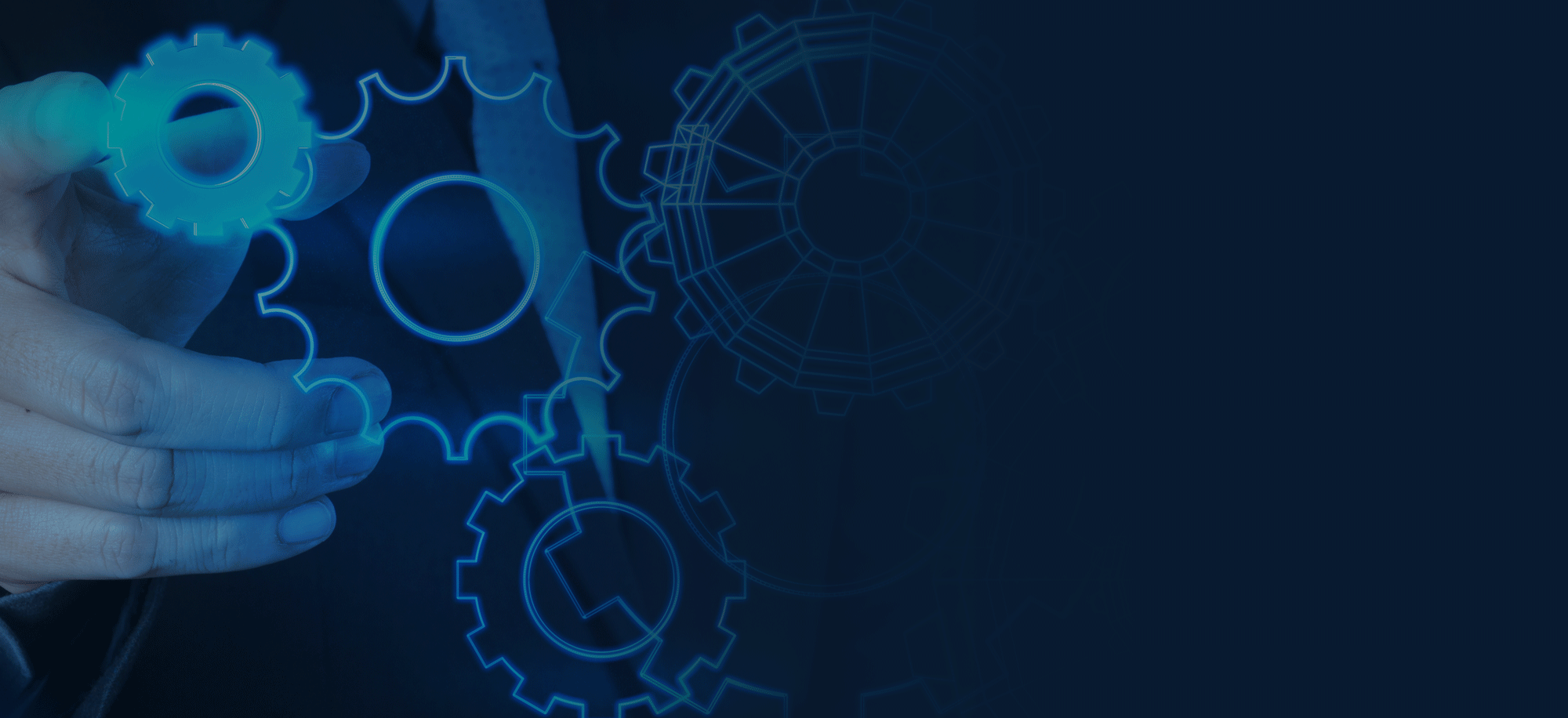
With IOT Process Quality Control, you will be able to verify that all production process operations are optimal, that machinery is functioning properly, and the correct production materials are being used to ensure quality. Additionally, it helps detect errors in the manufacturing process so you can make appropriate decisions, bringing efficiency to your operations.
Monitors the quality of lenses one-by-one
Allows you to inspect the quality of the lenses to ensure they meet a defined standard, detects errors in production and discovers areas for improvement.
Reliable and easy to use. No technical knowledge is required.
Step-by-step process. Displays the order of measurements by automatically highlighting out-of-tolerance values.
SPC* analytics tool
Provides statistical information on the quality of the production process. Facilitates data driven decision making to improve production and anticipate future problems.
Panels or reports. Five panels of statistical information to assist in tracking the production process.
Error tracking. Detect the area in the production process where the error is occurring and determine the steps to remedy the situation.
IOT Process Quality Control
We help you implement the proper quality control system for your production by offering personalized advice, flexible software configuration, quality controls, and process improvement.
* Statistical Process Control.
Information panels:
Status over time
Displays information about the quantity and quality of production, in a time series in relation to the target set for NO-GO lenses (lenses that do not meet the established quality standards).
Determining a target will help you to know the deviation from the desired goal.
It allows you to:
• Identify problems that occur on different days or at different times during production.
• Determine what causes the problems.
• Get an overview of the effect of the improvements introduced to improve quality.
• Know the production performance for each type of lens.
• Gather a large amount of information to improve the entire production process.
Number of lenses produced per hour day/week.
Percentage of NO-GO lenses produced.
Percentage of NO-GO lenses by material.
Percentage of NO-GO lenses by production stages and machine.
Type of lens design.
NO-GO analysis
Detects the causes of NO-GO production, establishing priorities by lens/material type, and identifying specific problems.
It takes into account that most errors are caused by a few factors. The NO-GO analysis detects these factors and focuses its analysis on them for each material. In addition, it identifies if the NO-GO percentage increases for a particular machine when a material is selected.
It uses prescription filters to determine if the error is affecting high or low prescription lenses, locates the materials and machines that are causing a significant amount of NO-GO, and detects if there is a correlation between two NO-GO characteristics.
For example: it narrows down the main problems with production, which materials are causing up to 80% of the errors, and which machine is responsible for them.
Number of NO-GO lenses by material.
Distribution of NO-GO lenses per stage and machine.
Percentage NO-GO in each evaluated feature.
Visual interactions showing distribution changes.
Improvement areas
Find the leading indicators that need attention in a easy way by classifying the type of lens and the main causes of error.
It makes a comparison between lenses with optimal performance. It analyzes the causes that may be affecting the rest to determine if the problem is specific by lens type, or if it’s due to a general problem, such as a malfunction of a machine that needs maintenance.
Number of NO-GO lenses.
Accumulative NO-GO.
Main analysis axis: material, machinery, and NO-GO features.
Comparative tool
Compare the performance of two different sets of lenses to locate errors by isolating machines, production lines, materials, or prescriptions, and simply make all possible combinations.
A simple tool that verifies if the conclusions obtained are valid. It applies filters to isolate, for instance, a set of lenses and proves if it’s the one causing the errors, determining its characteristics and aspects to be improved.
A very visual way to see a comparison between two sets of your lenses is carried out and, in addition, it allows you to determine which pieces of equipment have the best quality over time.
Daily or weekly evolution of the NO-GO percentage.
Lens details
Assembles a complete list of production information and allows it to be exported to a spreadsheet.
It locates a specific customer job, identifies the magnitudes of errors (deviations), obtains the customization parameters, and exports the data for any other type of further analysis.
Number of NO-GO lenses
Date - Material - Type of lens
Process - Machine - Status
Thanks to data analysis and machine learning techniques, IOT Lens Data Advisor maximizes the chances of success in each new fitting, increasing the patient’s final satisfaction. For the first time in the ophthalmic industry, an objective system that can learn and evolve over time – guided by wearers’ feedback – has been achieved.
The best lens is the one that meets the patient’s expectations and offers them the most satisfaction. However, today there are no comprehensive models or clinical studies available that provide a clear link between wearers’ satisfaction (with their personal characteristics) and those of the lens. The decision to recommend a design is generally based on the practitioners’ own experiences. It can be inferred by factors such as previous mistakes and successes, feedback from their patients, or other guidelines.
IOT Lens Data Advisor stems from the need to provide vision professionals with a system capable of calculating the best lens for each wearer based on objective data.
IOT Lens Data Advisor is an original patented solution. It is a pioneer in the use of machine learning in the ophthalmic lens industry.
IOT Lens Data Advisor includes a decision algorithm. A sequence of instructions that represents a solution model to calculate the ideal progressive lens, the one that guarantees high satisfaction. The algorithm considers aspects such as prescription, previous experience in the use of progressive lenses, lifestyle, and degree of satisfaction, among other factors.
IOT Lens Data Advisor grows and evolves by systematically learning from each new wearer. Thanks to machine learning (ml) techniques, it goes from being a static system to a living one, aimed at intelligently modeling the uncertainty associated with the patient. It considers their satisfaction, recognizing the variables that have the most significant impact on it and the design to be recommended. In this way, we manage to improve the current system, and wearers get even better lens designs.
Each patient has a unique profile in the IOT Lens Data Advisor platform with specific characteristics and needs, including their lifestyle, previous lens experience, expectations, prescription, proposed lens data, and their level of satisfaction. All this anonymous data, adequately organized and processed, generates a database used to detect patterns and behaviors, predict situations, anticipate decision-making, and calculate the ideal lens, offering the end customer a better experience.
Based on the satisfaction of previous patients, the system calculates lenses the wearer will like most by searching for profiles similar to their own: Lookalike Profiles.
Knowing a priori which will be the best lens for each wearer is possible. Thanks to the constant flow of wearers and with the appropriate machine learning techniques, we can create a lens that provides the greatest satisfaction. By analyzing previous wearers’ behavior and considering their satisfaction, IOT Lens Data Advisor offers professionals a system that calculates the correct lens design. It also helps to solve those cases with low satisfaction or rejection. IOT Lens Data Advisor is a breakthrough in providing better lenses for greater satisfaction and an improved wearer experience.
When executing a project with you, we like to get as involved as possible. Flexibility and customer orientation are crucial to us. You can count on our multidisciplinary teams for whatever you need. We answer your questions. We propose ideas, improvements, and innovations for your business.
As a matter of principle, we share our knowledge with you. This is the only way to refine even the most minor details of the products and technologies we develop together. Contact us whenever you need to. We are all ears.